ID Badge Design Guidelines
ID Badge Design Specifications and Guide
- ID Badge Print Technology
- ID Card Material
- RFID Card Printing and Design Issues
- Artwork Specifications
- Providing Artwork Files
- Color Matching
- Full Bleeds, Multiple Designs, and Color Coding
- Font Options
- Font Attributes and Auto-Reduce
- Badge Photos and Orientation
- Backside Printing
- Slot Punch Considerations and Tips
- Design Templates and Proofing
- Sample Badge Templates
- FILE to PRINT Individual Image Printing
- Production Print Preview (P3)
- ID Badge Technology Testing
- DURABadge™ Warranty
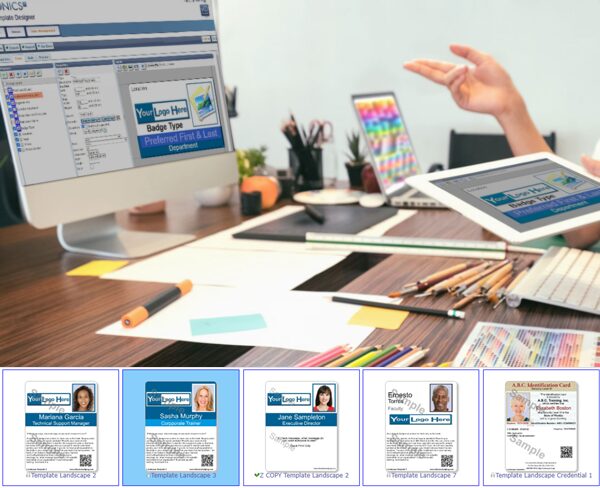
ID Badge Print Technology:
eXpress badging® uses the same dye-sublimation badge printer technology you would use if you invested in printing your badges. Dye-sublimation technology differs greatly from standard printing processes. If you design ID badges for your organization, you should know the best practices and potential issues. eXpress badging will integrate all the elements of your design. Below are our ID badge design guidelines for our process.

Dye-sublimation Printing
IDP Smart 81 Printer
Dye sublimation Printing Discovery
Slight imperfections due to the dye-sublimation printing process are acceptable. Dye-sublimation PVC card printing and lamination cannot produce blemish-free badge prints and lamination 100% of the time. Minor imperfections that do not affect the appearance from a distance are considered acceptable.
Acceptable Printing and Lamination Imperfections Include:
- Fine debris and lint particles trapped under the print film and laminate that are not in the photo, text, or logos.
- Variations in the white shade of the PVC card stock over time and by technology type.
- Slight color variations due to changes in printing technology upgrades that are not noticeable from a distance.
- Printed names that extend to the very edge of the card but are not truncated.*
Not Acceptable Printing and Lamination Imperfections (Cause for Reprint):
- Printing imperfections, embedded particles, debris, or lint within printed areas that are noticeable from a distance.
- Lamination debris or air bubbles between lamination layers that are noticeable from a distance.
- Printed names that extend beyond the edge of the card or are truncated.*
*Any truncation caused by exceeding max field length when auto-reducing font size is requested to be disabled/turned off is deemed acceptable by eXpress badging.
Considerations for eXpress badging “Standard” Badge Format or Non-Laminated Badges:
- Image fading caused by extended sun exposure can occur within weeks or months and is not covered under warranty for fading, cracking, or breaking.
- Barcodes are not warranted and will wear off much quicker (within weeks or months) in the “Standard” format badge.
When an eXpress badging DURAbadge™ formatted laminated badge image fades, cracks, or breaks within 24 months of the ship date, refer to the DURAbadge™ warranty below.
ID Card Material:
eXpress badging prints on PVC card stock material for photo ID badges. The white opacity of cardstock will vary between “standard” 100% PVC and “composite” 60% PVC and 40% polyester blended cards. Over extended periods, the white contrast of PVC cards cannot be guaranteed due to variations in the card manufacturing processes and material used.
We have other material options for special projects, and oversized cards are considered custom.
- Technology Cards: RFID, Magnetic Stripes and Barcodes
- Lamination for added durability and fade protection
- Adhesive Stock
- Tri-modal Security Seals
- UV Inks
- Foil Stamping
RFID Card Design and Printing Issues
The surfaces of most RFID cards have irregularities that can cause printing issues over the raised chip and antenna areas when using direct-to-card (DTC) PVC printers. Designing around the RFID antenna zone will avoid these issues. You can use a mobile phone flashlight to locate the antenna zone on the card.
For extended durability and high-quality printing, reverse-transfer printers and composite 60/40% format cards are also suggested. Laminating the card with a 1MIL patch on each side can provide even more durability and reduce card fading due to sunlight exposure. Contact your ID Specialists for assistance!
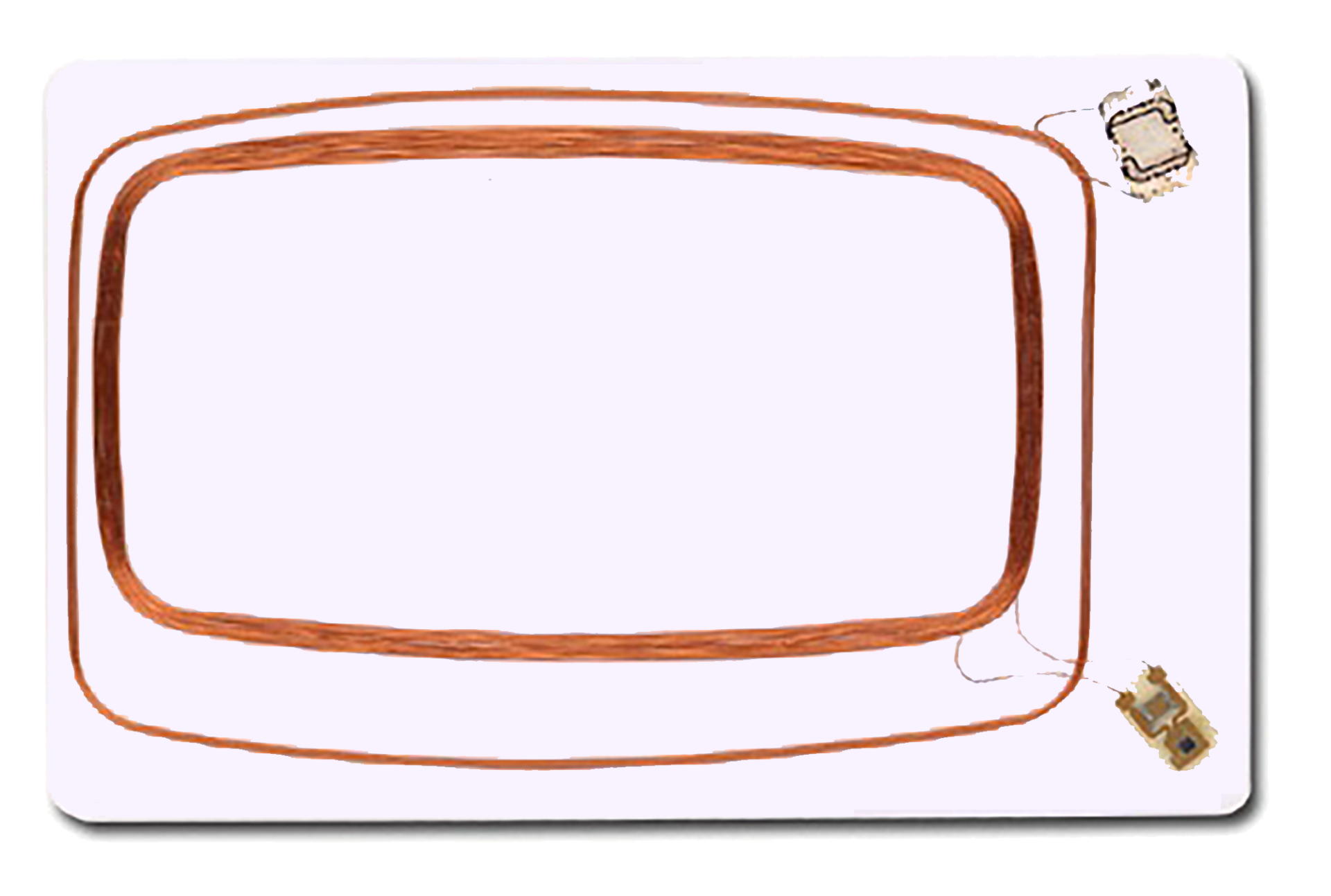
Duel 125 kHz Proximity and
13.56 MHz Mifare® PVC Card
Artwork Specifications
Image Specifications for Badge Designs:
- Providing high-quality artwork for your logo, service marks, photo images, trademarks, and company colors is best.
- Poor quality artwork may require professional services by eXpress badging to clean up artwork for a fee if needed.
- Please provide the static graphics file used for import into our system’s badge template.
- The final graphic/s must not include variable text and/or photos unless it is a layered PSD Microsoft Windows file format.
- Additional sample files with text and photo illustrations can be supplied.
- Source artwork is preferred.
- Contact your marketing department regarding obtaining current artwork files and branding guidelines tom share with eXpress badging.
Preferred File Type:
- The image you submit should be in a transparent PNG format and saved in RGB color mode.
- We also accept files in JPG, PSD, PDF, TIFF, and BMP formats.
- The recommended resolution for graphics is 600 DPI.
- Please provide layered PSD or PDF files if you submit the entire badge design.
- We will disable the photo image, names, slot marks, and corner rounds/marks to create the background merge template.
- Other printed elements specific to individual associates will be added separately and set to print when certain conditions are met.
- For example, if the Certification Field is “Forklift,” the forklift_cert_I.jpg image will be printed.
- To maintain quality, graphic dimensions should match the exact size for printing, with no more than a 25% increase/decrease in size.
- For your reference, the standard badge size is 3.375” x 2.125” (3-3/8” x 2-1/8”).
Mouse Over For Data and Photo Merge
Providing Artwork Files
eXpress badging has several methods for delivering artwork:
-
Use our ID Badge File Upload Center
-
We can set up a secure ShareFile Account for those with artwork files over 10MEG.
-
Our team can pull artwork off of your FTP server.
Color Matching:
When it comes to matching your company’s colors, we will make every effort to closely match them. However, it may not be possible to precisely match the Pantone Matching System (PMS) numbers. Also, please be aware that colors may vary based on the printers used, so differences in color may occur over time due to changes in printer technology and upgrades. Teal and Burgundy are particularly difficult colors to match closely and may require additional costs.
Please keep in mind that the colors on a computer screen or printed from your printer may not accurately represent the final printed color. The final product color may differ from the RGB, CMYK, or PMS numbers provided due to the heat used in the dye-sublimation printing process and variations in industry standards.
For organizations in need of precise color matching for ID badge production, custom-printed stock must be pre-ordered. This process requires a 20-business-day lead time and may incur additional costs.
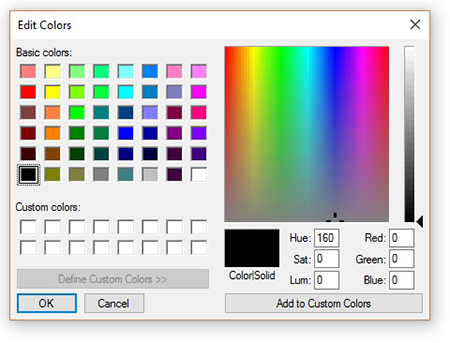
Color Palette and Matching
Full Bleeds, Multiple Designs, and Color Coding
Full-bleed Designs:
Direct-to-Card PVC badge printers do not print over the card edges, which are the standard printers used if you were to print in-house. A thin white line border may appear on some edges that “bleed” over. We suggest placing a .05″ margin border around images that print to the edge for best results. eXpress badging has a small fleet of direct-to-card printers, so we can match rebadging projects with badges printed onsite by our customers.
eXpress badging primarily uses a line of High-Definition printers (600DPI) for projects that require edge-to-edge printing and higher-resolution graphics. In this case, your badge design files must account for the bleed of .125″ on each “bleed” side.
Multiple Designs and Color Coding:
If you have more than one badge design or are using color coding, you’ll need to provide a cross-reference stating what data field(s) is being used (badge type, department,…) to select the design or color that is assigned to each for example: in the “badge type” field employee=blue, contractor=yellow, temporary=red…).
Mouse Over For Full Bleed Preview
Fonts:
To ensure consistency across different badging management software platforms, eXpress badging uses Arial as its default font and recommends that you do the same. Using a different font for your variable data might not be noticeable to most people and could make it harder for others to read. However, for badge design static text, you are free to use your preferred font.
We do offer a limited selection of other fonts if Arial is not suitable for your needs. If you need to use a specific font, please provide the font name, font files, licensing agreement, and formatting information. Please note that additional costs may apply if font licensing is required by eXpress badging for the font you request.
Font Options
Font Attributes and Auto-Reduce
In general, the fonts for all merge fields (such as first name, last name, title, department, etc.) are automatically adjusted to fit within the defined text area. This means that longer entries will be printed in a smaller font size to prevent cutting off the text, while shorter entries will be printed in a default larger size for better readability.
If you prefer the font sizes to remain the same regardless of text length, you’ll need to figure out the maximum character length before the text gets cut off, and then input your badge data accordingly. Your badges will be printed exactly as entered, whether the text gets cut off or not, and if you need them to be reprinted, you will need to cover the cost.
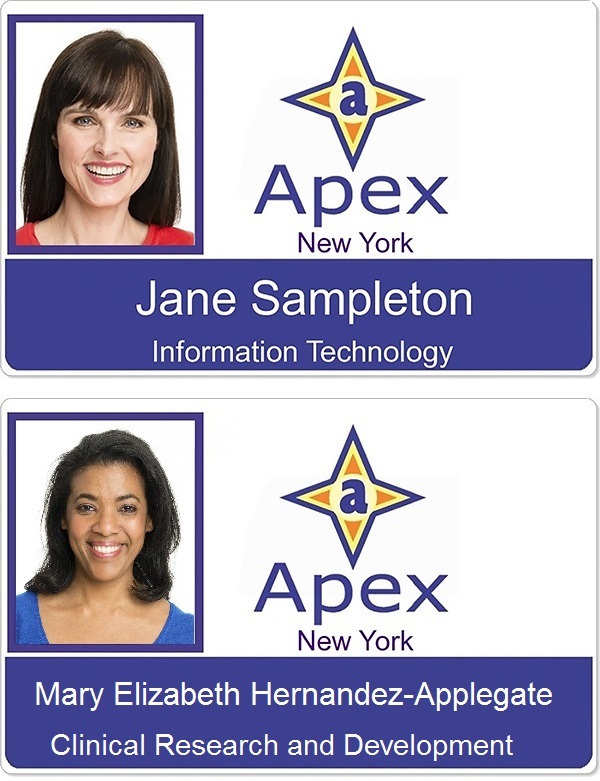
Auto-Reduce Font Atribute
Badge Photos and Orientation
- We suggest using cropped rectangular headshots that show the entire employee’s face with minimal background visible.
- The standard industry size for a badge photo is 1″ x 1.25″.
- If you choose different dimensions, it may affect previously captured images and their appearance.
- Previously cropped images are converted to low-resolution images, which can cause issues when resizing.
- Please note that we are unable to convert square-cropped photos to rectangles.
- We provide oval and circle photo printing.
- For ovals, we use rectangular-cropped photos.
- For circles, we use square-cropped photos.
- The corners of circular photos will not be printed.
- We recommend using color bars and thick borders for easily identifiable and noticeable color codes.
- We do not recommend using color photo backgrounds.
Mouse Over For Photo View Options
Backside Printing:
By default, badges are printed in black only on the back. There are no grayscale options available, as they will appear pixelated. Please provide your backside text information in an MS Word or text file. While we can print in color on the back, be sure to upgrade your project to include color back printing as it increases the cost.
If nothing is printed on the back of your badge, ask your team this question: “The back of our badge is like a billboard on a busy highway, and it will be looked at many times without delivering any message; so what message would make this valuable real estate to our organization?” If you end up with nothing, then leave it blank.
Mouse Over For Color Back View
Slot Punch Considerations and Tips
Most photo ID badges are slot-punched to be used with a badge holder (clip, lanyard, or reel). When designing the badge, it’s important to consider the slot location. The standard offset of the slot is 0.25″ from the bottom, centered on the top edge. The standard slot width ranges from 0.55″ to 0.625″, and the standard slot height is 0.15″.
Design Considerations:
- When designing both the front and back of a photo ID badge, it is best to add a slot placeholder so you can design around it.
- Ensure that once slotted, it does not cut into logos or placed text
- Turn off the slot placeholder when saving the final badge background template.
- Otherwise, it will be printed, and portions may appear of the printed and slotted badge.
Other Consideration:
- To prolong the life of the slotted area, consider using composite PVC card stock, which is more flexible and can withstand temperature changes and damage caused by sunlight. Upgrading to a laminated badge will prolong the life even more. Both features will eliminate the need for plastic badge holders.
- RFID cards can be slot-punched, but it’s crucial to know where to punch them. Most RFID cards have printed hash marks in either portrait or landscape formats. Some cards can only be punched on the shorter edge in portrait orientation. However, lower-quality RFID cards may not have hash marks. In this case, you can use a mobile phone flashlight to locate the antenna edges and determine where to punch. It’s important not to assume that all cards were packaged with the orientations all the same, so be sure to check each one individually.
Mouse Over For Slotted Badge
Design Templates and Proofing:
eXpress Badging will import your logos and create a badge template with data merge fields for printing based on the template and design setup you selected and approved. This is an industry best practice. If you have already designed your badge according to the required specifications, please deactivate all variable data elements, photos, slotting, outlines, etc., so that only the design template is saved as specified in our artwork section above. eXpress badging will incorporate the merge fields and photos within our badge template using the fonts stated above.
Proofs
eXpress badging will send formal proofs for the customer’s digital signature within two to three business days of receiving the order, associated artwork, and graphics files (if applicable). The proof process is not a stage for designing the badge; it does not allow for multiple changes to determine the final look of the badge. If a customer is unsure about the design of the ID badge, they should work with their ID Specialist to provide a preliminary mockup. We can email hyperlinks for quick review. Once the proof is approved, eXpress badging can mail Production Proof samples for final review. Production Proofs are usually mailed via USPS First Class unless expedited shipping is requested and paid for by the customer. Proof fees are charged to the customer for new badge designs and for previously approved designs that require edits.
Before proof approval, have more than two authorized and qualified individuals review it. Once an authorized customer representative approves the proof, eXpress badging requires it to be digitally signed via a provided link or printed/signed/scanned version that is emailed back to eXpress badging. The customer signed and approved proof transfers the responsibility of proof accuracy to the customer’s signer. Any reprints required after proof approval due to noted errors or edits will be at the customer’s expense. No exceptions!
Customer at-fault issues:
- The customer approves the design proof that contains an error(s)
- The customer provided the wrong ID numbers for eXpress badging to encode/clone from
- The customer provided the wrong photo assigned to an ID number
- The customer approves non-approved Portal records (data and/or photos) for printing
- The customer provides an incorrect badge type (different locations have different systems and therefore different badge types)
- The customer makes a design change after the approval of the proof
Basic Template Design
- Customers select a design template on our website (scroll down from here).
- You’ll be provided a preview of a virtual ID.
- Basic Templates are designed for those who do not require design control and either minor edits, or none at all.
Basic Template Edits
- If you require any edits to the template they must be submitted at the time of your file drop submission
- Otherwise, a design change fee will be charged ($25.00).
- Edits can only be
- Font type, font and photo border color, and font size: be specific.
- Take the time now and determine how you want the design to look.
- Copy the template (Print Screen), paste and edit in MS Paint, and type out all edits.
- Save it in JPG format and provide the file with your file drop.
- We do not provide formal proofing for approval other than a URL preview.
- More than one edit with a preview will require a $25.00 design change fee per occurrence.
- If you have specific design requirements, you’ll need to upgrade to our Standard Design service, which costs more and provides more design options and edits along with digital proof for sign-off.
Standard Template and Custom Design
- eXpress badging prints an actual ID badge and provides a scanned image proof for approval and sign-off.
- Customer-provided badge designs serve as the guide for proofing and are used by eXpress badging to create the final ID badge template, providing an actual representation of your finished badge.
- Printed samples can be mailed upon request.
- Your approved proof approval must be received before ID badges can be printed.
Mouse Over For Design Template
and merged ID badge.
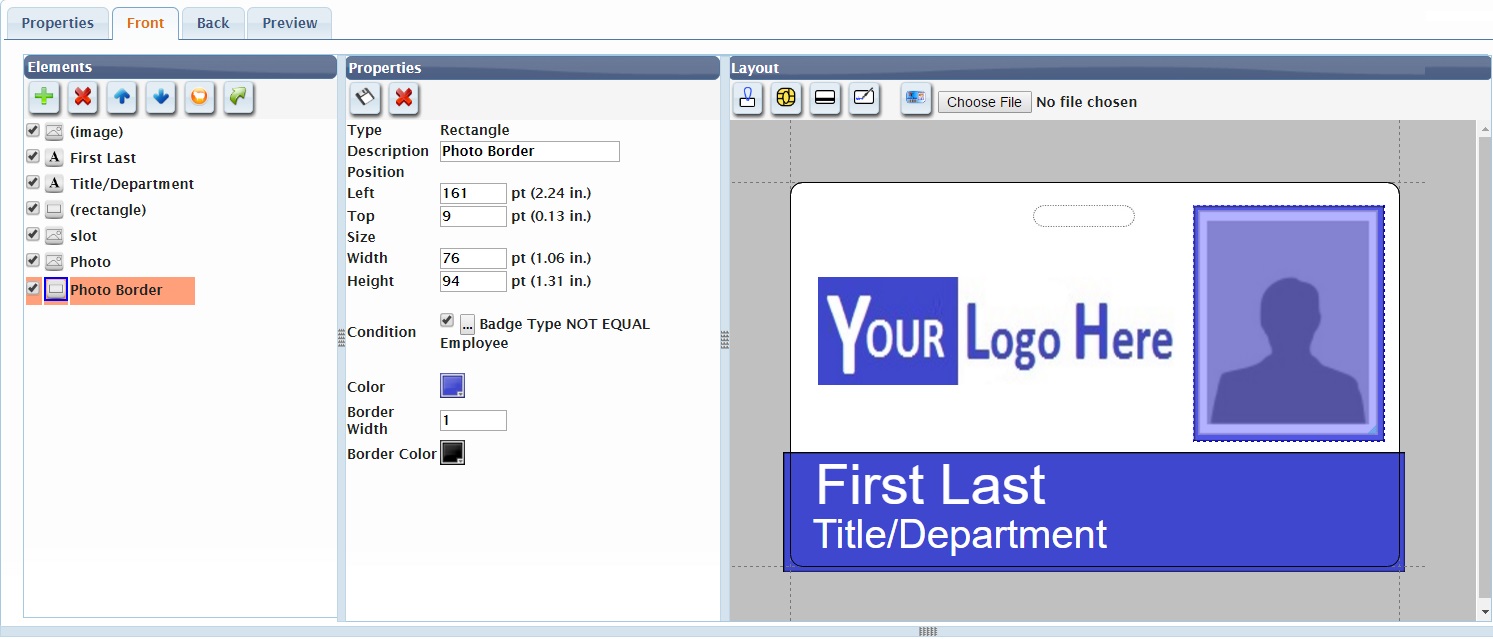
Badge Template Designer
with Merged Elements
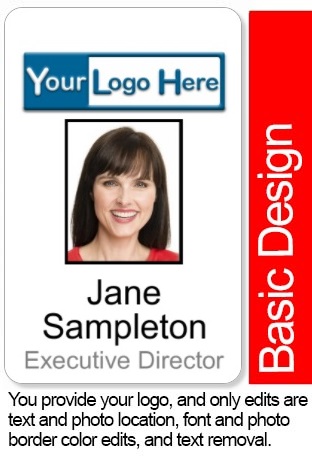
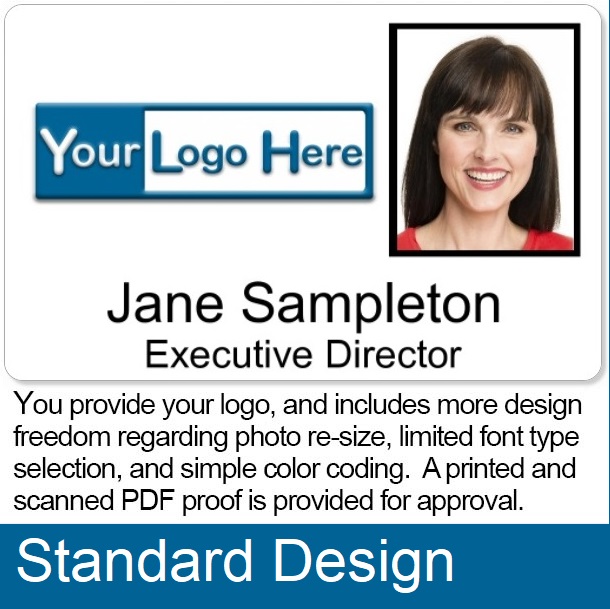
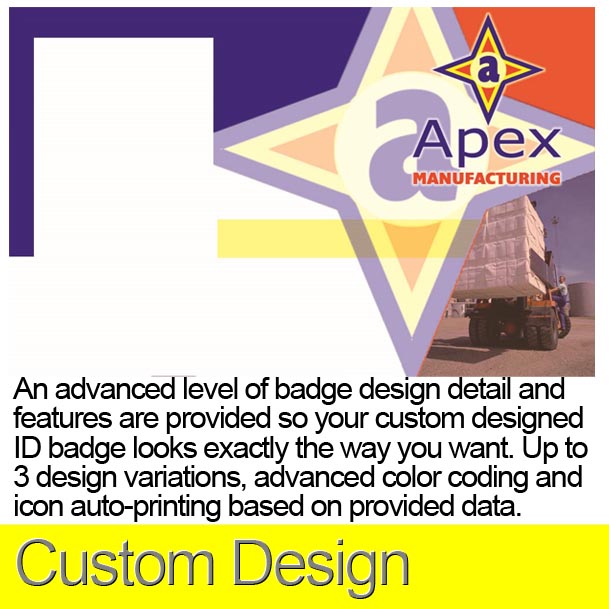
FILE to PRINT Individual Image Printing
For customers who want to provide a completed graphic design for their ID badges, we offer our FILE to PRINT service. Please note that we do not make any edits to customer files. Files will be printed exactly as they are sent.
To avoid receiving a poor-quality print, follow the steps below.
Please note that providing finalized files for printing photo ID badges is not the typical process. We recommend using our design merge template process, where you provide the badge design background file without the photo and data, utilizing one of our templates for placement. We will then import the data and photo merge elements for printing. After that, you only need to provide a spreadsheet and data or use our Portal to enter, upload, and preview each badge before submitting it for printing. This approach ensures higher print quality and is simpler to manage.
FILE PROPERTIES
- JPG and PNG files only: convert all PDF, PSD, AI, and other files
- 600 DPI using RGB configuration
- If you want the files printed in a sort order, use a naming convention that is sortable: last_first.jpg or .png
- Use our ID Badge File Upload Center to provide individual JPG/PNG images or zip file
BADGE DIMENSIONS
- Landscape badge must be 3.475” x 2.225”
- Portrait badge size must be 2.225” x 3.475”
- Print Zone is L = 3.375” x 2.125” or P = 2.125” x 3.375”
- No Print Zone is .05″ of the surrounding border
BADGE DESIGN
- Visit our Template Library for starting designs
- Leave room for slots at the top of both sides of the badge
- Do not include slot location marks or border edge lines; they will be printed
- Save with the design image with square corners if the design bleeds off the edge
- Do not use fonts smaller than 6 points, they will not print clearly
- Solid backs look great but will show more card printing imperfections
TOO MUCH TIME TO FORMAT FILE TO PRINT?
- Send the background file with no data or photos
- Provide a spreadsheet of data
- Provide group or zip files of photos
- Use our Proofing Process to guarantee your badge design is perfect
- We will merge-print your badge print job the correct way, with less work on your side
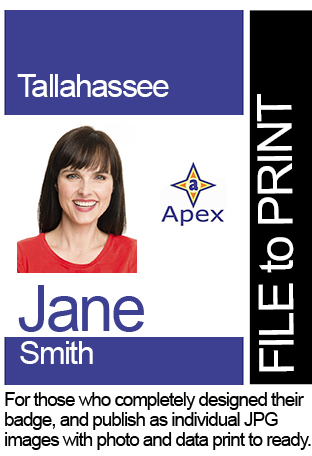
Production Print Preview (P3):
For larger projects that have multiple badge designs or want to preview the entire print job before printing, eXpress badging offers a Production Print Preview we call a P3. This is a recommended step when printing on RFID stock to ensure it is printed correctly the first time. We print the entire order to PDF and securely provide the file as a Print Job Proof, and we require signoff just as we do with the badge design proof. Once approved, eXpress badging prints the job as provided within the P3.
The P3 addresses a few concerns:
- Are the photos assigned to the correct record, or are photos missing?
- Are the photos cropped to the correct aspect ratios and standards?
- Are the photos cropped to standard correctly?
- Is the record data correct and prints the correct badge template?
- Is the sort order correct?
The P3 is not a design-proof tool and is used only for data/photo verification only.
If badge design corrections are required in the P3 stage, and proofing was approved; the approved proofs are voided, and the project is paused until the badge design corrections are re-proofed and approved.
FREQUENTLY ASKED QUESTIONS
Q: My badges do not look like the badge proof we approved looks.
A: A P3 is not meant to represent the final look of printed badges. This file is not intended to be used for design changes.
Q” Why does my P3 look off-center?
A: Your badges are constructed in software meant for printing physical badges, not authoring PDFs. Printed badges will be centered, straight, and true.
Q: Why is the upper margin larger than the lower?
A: Your badges may be slotted for use with a clip or lanyard and, as such, require extra space for the hole.
Q: Will my badges have round corners?
A: Yes, your printed badges will have round corners
Q: I noticed an error; what should I do?
A: Let us know! But first, please review the rest of the P3 so that we can make all corrections in one pass. Orders requiring additonal P3’s will be assessed a fee of $25 per additional P3.
ID Badge Technology Testing
In addition to the design and proof process, eXpress badging requires technology testing and sign-off for any cards used in a badge reader system. This ensures that the ID badges produced by eXpress badging will work in all your systems. Sample test cards are provided based on customer specifications. Test cards must be enrolled in each system used, and then transactions are generated for each test card provided. We recommend printing a transaction report in each badge reader system to document successful ID badge enrollment and transaction generation (the badge works in the reader). The report should indicate whether the badge opens the door, records a time punch, records a tracking transaction, and records the transaction in the system using the unique badge ID number and the person assigned to it.
Testing guidelines:
- Start by identifying all badge reader systems in use. Provide the manufacturer’s name, the integrator/dealer information, and the point of contact for each system.
- Take a photo of your RFID card box label and/or back of the card and email it to your sales representative.
- Identify the systems used for:
- Time and Attendance
- Access Control
- Tracking Systems
- Point of Sale
- Document the reader type and specifications for each technology used:
- RFID Proximity (125kHz)
- RFID Contactless (13.56 MHz)
- Barcodes
- Magnetic stripes
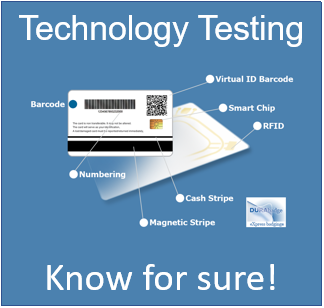
DURABadge™ Warranty
The “Standard” PVC badge by eXpress badging does not come with a durability warranty. If you use the non-laminated “Standard” format badge, the image may fade due to extended sun exposure within a short period, and such fading is not covered by warranty. As the “Standard” format badge ages, it may become more brittle, leading to cracks in the slotted area or even the entire card breaking. Barcodes on the “Standard” format badge are not warranted and may wear off quickly.
The DURAbadge™ formatted badges, which have a 1MIL over-laminate on each side, will last much longer and come with a two-year warranty. The warranty covers badge cracks, slot punch area breaking, badge breaks, and images on any laminated side due to regular card use. This warranty starts from the date of order processing/shipping.
eXpress badging’s Warranty Procedure:
- The badge must have been produced by eXpress badging within the last 24 months and meet the terms mentioned above.
- If there is an issue, take a photo of both the front and back of the badge and send it to eXpress badging’s production department.
- Wait for eXpress badging’s approval acknowledgment before destroying the badge. They may request that defective badges be returned at their expense.
- If the badge technology stops working, eXpress badging may provide a self-addressed/stamped return envelope for evaluation or ask that the defective cards be destroyed.
- If you have any questions regarding our design process or the above guidelines, feel free to ask. Please contact our ID Specialists for assistance!
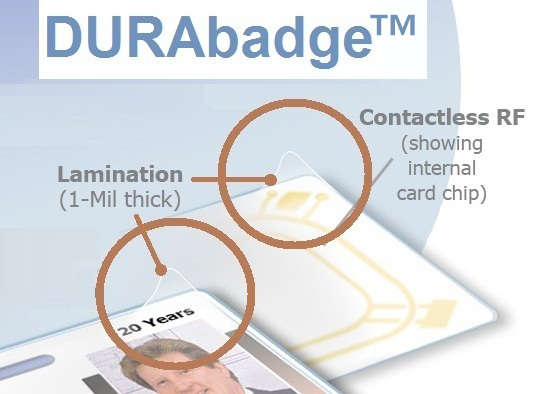